This combination of spacers was recently used on the Beetle chassis. I measured the distance between the bushings. Then measured the crown thickness. I was very lucky in that the numbers were close enough without having to use too many spacers to take up the gap. The exact right number.
They are sitting in order of how they sit on the axle.
2mm brass and an 0.010″ inch steel spacer. Crown gear. 1.5mm brass and 2 x 0.005″ inch steel spacers.
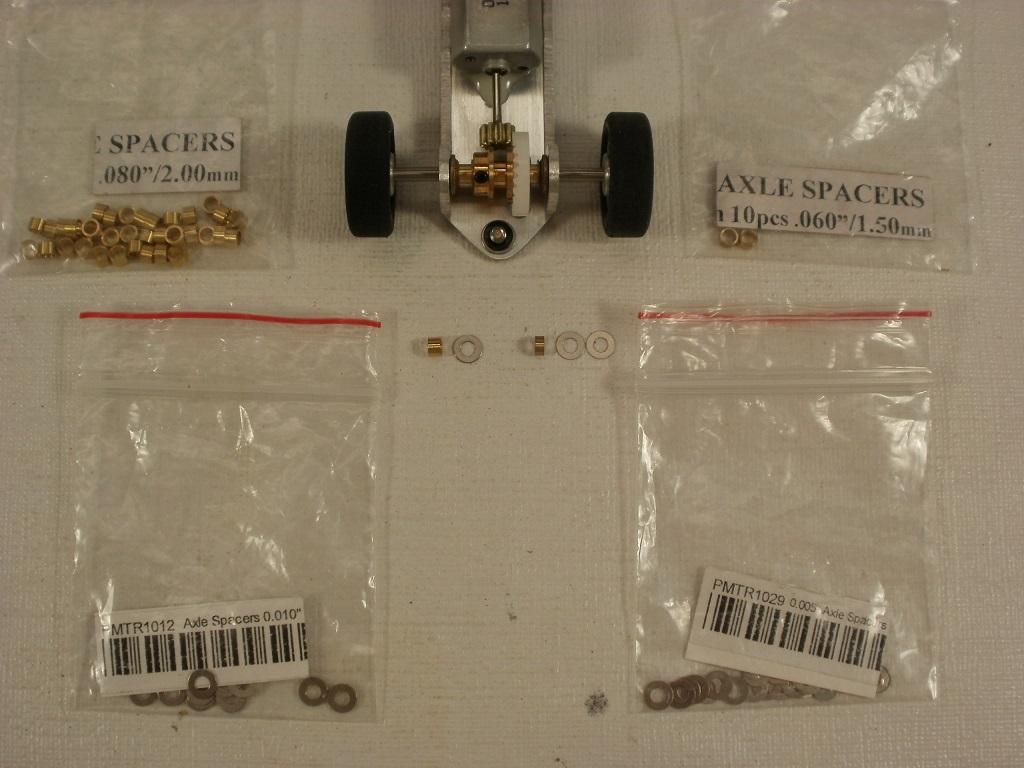
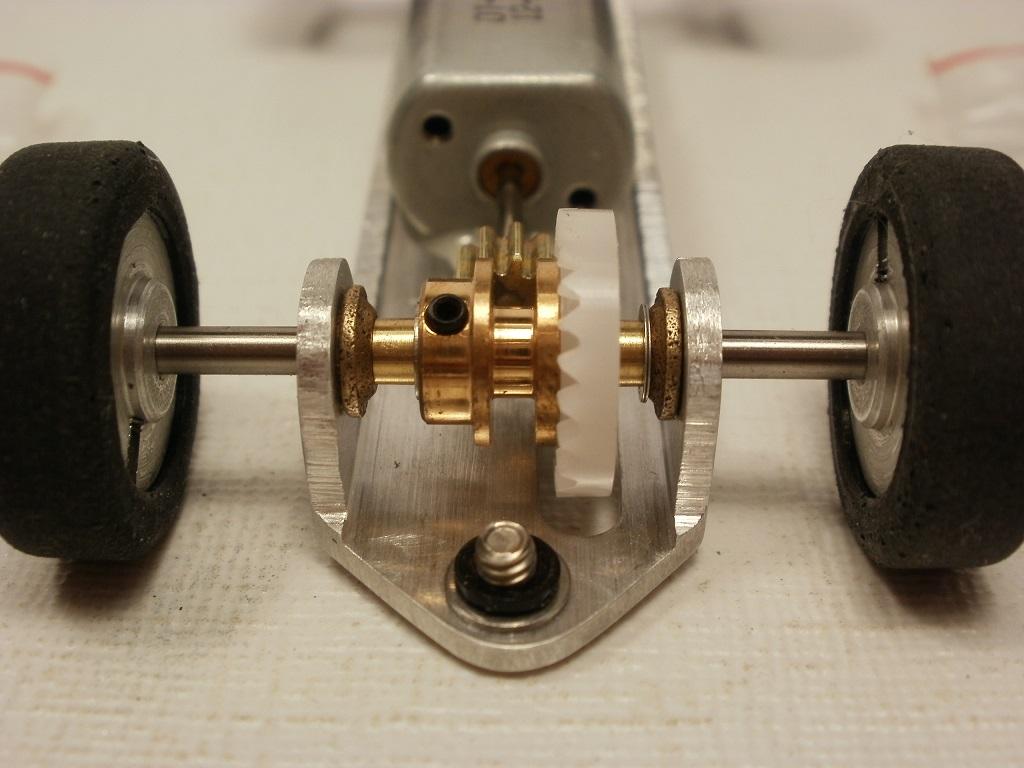
Before gluing the motor in, the 0.010″ spacer was installed on the same side as the 2 x 0.005″ spacers. The motor was epoxied in place holding the gears tight to each other. After the 5-minute epoxy hardened. The axle was removed, and re-installed with the 0.010″ washer on the other side to create an exact gear mesh clearance.
The crown has raised letters that can interfere with measuring it. So I sand it smooth with 400-grit paper on a flat surface. I make small circles so as not to sand any side down more than the other.
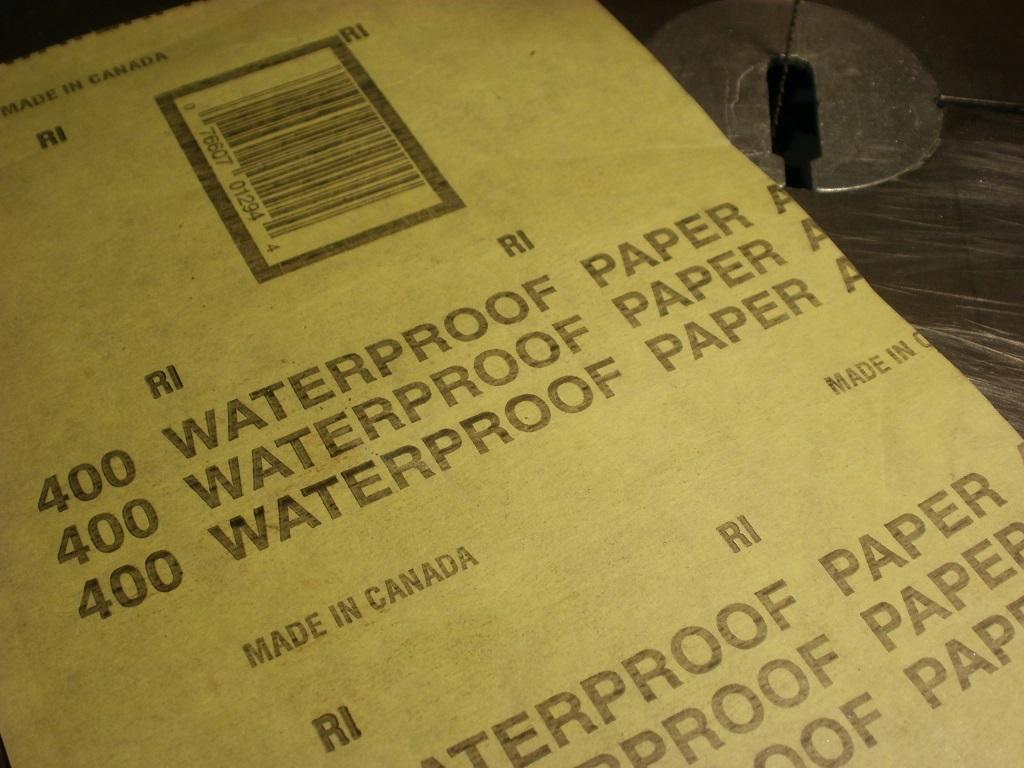
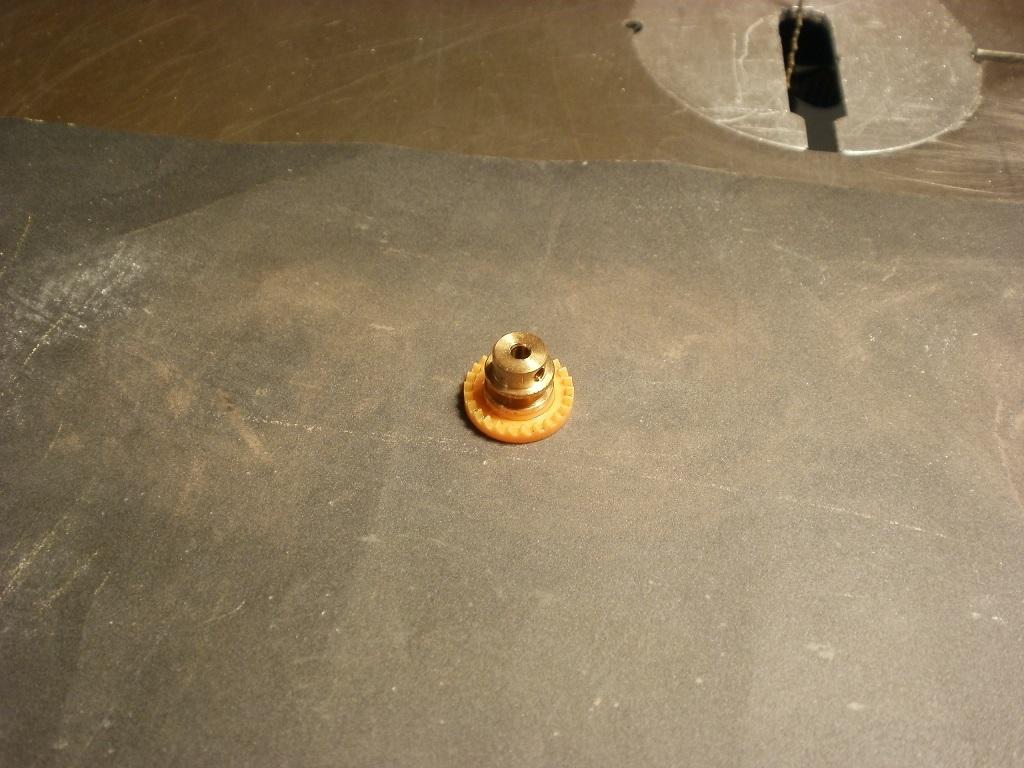
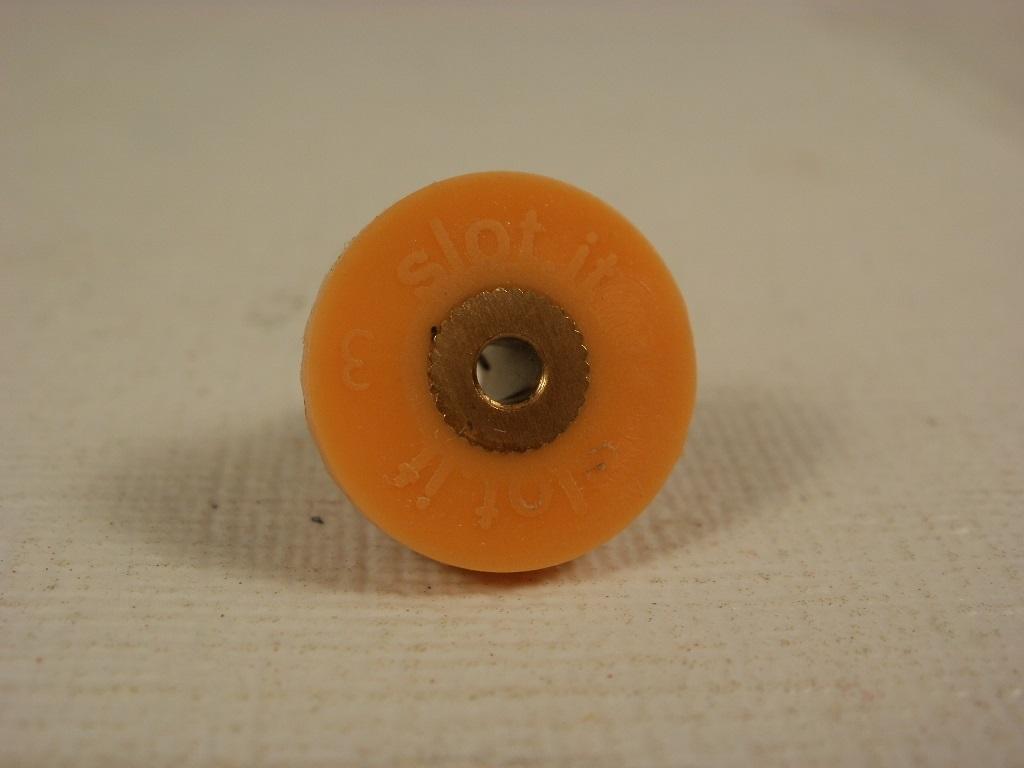
What I found by mistake is that you can easily take a tenth of a millimeter off the width of the crown to help it fit better.
Use the least amount of spacers as possible during assembly. They can have a bit of a spring-like reaction in larger numbers.
Best regards,
Ken